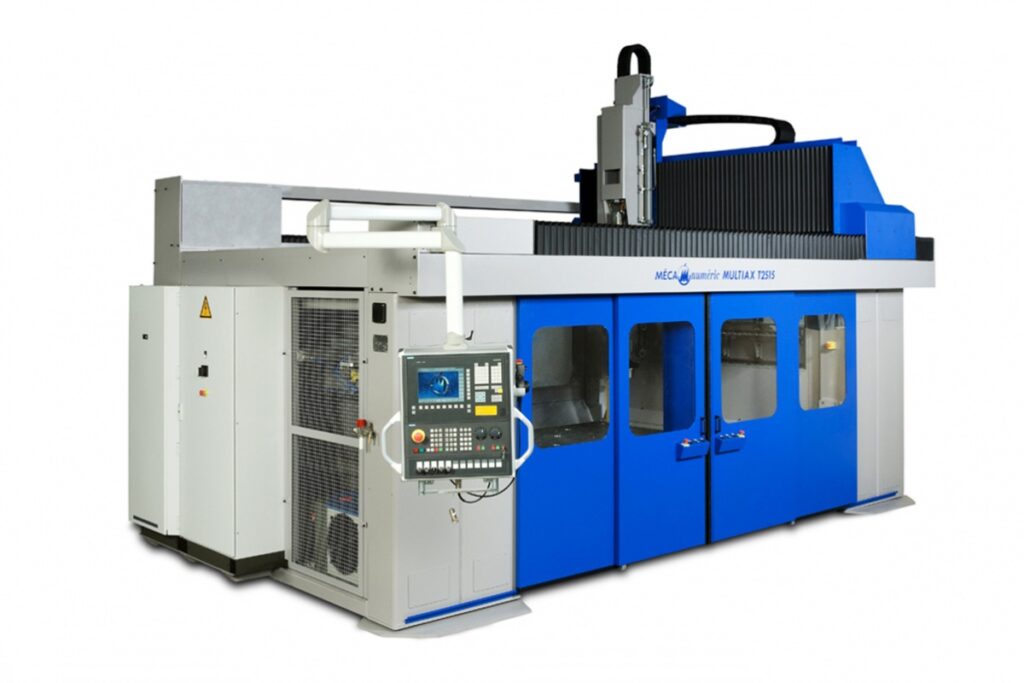
CNC machining is known for precision, repeatability, and the ability to handle complex geometries—but that precision comes with cost.
Whether you’re developing prototypes or full-scale production parts, controlling CNC machining expenses without compromising quality is essential to product success.
Design choices have a direct impact on machining time, tooling wear, setup complexity, and material waste. By making your parts more machining-friendly, you can significantly lower costs without affecting function or tolerances.
This article offers actionable design tips to reduce CNC machining costs while maintaining high quality—backed by real-world practices used in aerospace, medical, and industrial manufacturing.
1. Optimize Geometry for Machining Efficiency
Complex geometry increases programming time, tool changes, and cycle duration.
Simplify designs where possible to reduce unnecessary complexity. Features like deep pockets, tight inside corners, and intricate curves slow down the process and may require custom tooling or multiple setups.
Design Strategies:
-
Use standard radii: Internal corners should have a radius of at least 0.8–1.0× the tool diameter
-
Avoid deep cavities: Keep depth-to-width ratio under 4:1 to minimize deflection
-
Limit sharp internal angles: Use fillets to allow smoother toolpath transitions
-
Consolidate features: Combine surfaces and eliminate unnecessary operations
By simplifying geometry and aligning it with standard tooling sizes, you allow for faster, cheaper, and more predictable machining.
2. Design for 3-Axis Machining When Possible
Multi-axis machining is powerful but more expensive.
While 5-axis CNC machining can reach complex surfaces and internal angles, 3-axis machining is generally cheaper and faster due to simpler fixturing, shorter toolpaths, and faster programming.
Tips:
-
Orient parts to allow complete machining from one or two sides
-
Design features to be accessible with vertical or horizontal cutters
-
Avoid undercuts unless necessary
-
Choose symmetrical shapes that reduce repositioning
If your part requires 5-axis machining for only one feature, consider redesigning that section to be a secondary, attachable component.
3. Select Machining-Friendly Materials
Material choice affects tool wear, feed rate, cycle time, and overall cost.
Harder or more brittle materials like titanium, Inconel, or hardened steels require slower cutting speeds, specialized tools, and more frequent tool replacement. Softer and more common materials like aluminum, brass, and plastics are more affordable to machine.
Material Cost-Efficiency (general ranking):
Material | Machining Cost Impact |
---|---|
Aluminum 6061 | Low (easy to machine) |
Brass | Low (non-ferrous, stable) |
Stainless Steel | Medium (requires cooling) |
Titanium | High (slow feed, tool wear) |
PEEK | High (requires sharp tools) |
Inconel | Very High (heat-resistant) |
Always weigh mechanical requirements against machining costs. If a part doesn’t need aerospace-grade strength, consider switching to an easier material.
4. Use Standard Hole Sizes and Threads
Non-standard hole sizes require custom tooling or additional operations.
Keep hole diameters compatible with standard drill bit sizes and avoid excessive tap depths.
Best Practices:
-
Use standard drill sizes (e.g., 3 mm, 6 mm, 10 mm)
-
Limit tapped hole depth to 2× diameter
-
Avoid threads in blind holes when possible
-
Use unified thread sizes (UNC/UNF or metric) across the design
Also, avoid placing holes too close to edges or walls, as this can cause tool chatter, deflection, or poor surface finish.
5. Minimize Tolerance Stack-Up
Tighter tolerances increase inspection requirements, tool precision, and scrap risk.
Apply high-precision tolerances only to critical functional features (e.g., mating surfaces, press fits). Leave general-purpose surfaces with standard tolerances (±0.1 mm or even ±0.2 mm where allowed).
Cost-saving tolerance strategies:
-
Apply ±0.005 mm only where function demands it
-
Use general GD&T callouts (like flatness or concentricity) instead of specifying every face
-
Avoid stacking tight tolerances across large assemblies
Over-tolerancing is one of the most common ways designers unknowingly increase part cost.
6. Reduce Setup and Fixturing Requirements
Each setup change adds time, labor, and potential error.
Multi-sided parts that require repositioning or custom fixturing are more expensive to machine.
Tips:
-
Design for single-setup machining
-
Use self-locating features (e.g., datums, dowel holes)
-
Keep part symmetry to reduce orientation changes
-
Avoid part geometries that require custom jigs or holding solutions
Minimizing setups shortens machine idle time and improves consistency across runs.
7. Avoid Excessive Surface Finish Requirements
Surface finish (Ra) requirements directly impact machining speed and cost.
Polished or mirror-like finishes may require slower feed rates, additional passes, or even secondary processes like polishing or grinding.
Guidelines:
-
Use Ra 3.2 µm (standard machining finish) unless a smoother finish is necessary
-
Avoid specifying Ra < 0.8 µm unless for sealing surfaces or cosmetic zones
-
Apply surface finish specs only to critical zones—leave others at standard finish
By specifying finishes selectively, you reduce unnecessary machining effort.
8. Prototype Early to Validate Cost-Effective Designs
Prototyping helps you identify cost drivers before committing to large-scale production.
A single CNC prototype can reveal:
-
Whether tolerances are too tight
-
If features cause excessive tool changes
-
How long cycle time is in real-world conditions
-
Opportunities to consolidate or simplify
Collaborating with a CNC machining service during early development ensures that cost optimization is built into the design—not tacked on later.
9. Label Parts Digitally Instead of Machining Engravings
Engraving part numbers or logos directly into metal adds time and requires specialized tools.
If labeling isn’t needed for function or regulatory compliance, consider alternatives:
-
Laser engraving (faster and cheaper)
-
Stickers or ink markings (for internal parts)
-
QR codes or serialized labels on packaging
Only machine engraving when absolutely required—such as for serialized medical components or aerospace traceability.
10. Communicate with Your CNC Provider
Open communication with your CNC partner can lead to smarter designs and lower costs.
Experienced machinists and CAM programmers can spot inefficiencies, suggest toolpath changes, or recommend better materials.
What to ask your machining provider:
-
Can this feature be simplified without affecting function?
-
Are there alternative materials that are easier to machine?
-
What tolerance should be applied here?
-
Will this design require multiple setups?
Engaging early, especially during prototyping, ensures the final part is cost-effective without compromising performance.
Summary: Cost-Saving Design Tips at a Glance
Design Element | Optimization Strategy |
---|---|
Geometry | Simplify; use standard features |
Tolerances | Tighten only where necessary |
Materials | Choose easy-to-machine options |
Setups | Minimize repositioning and fixtures |
Surface Finish | Limit Ra specs to critical areas |
Threads and Holes | Use standard sizes and depths |
Labeling | Use digital or laser markings |
Final Thoughts
Reducing CNC machining costs doesn’t mean cutting corners—it means designing smarter.
By aligning your part design with machining capabilities, you reduce complexity, avoid unnecessary operations, and improve efficiency at every stage.
Start applying these design strategies early in the development process to avoid costly redesigns or production overruns. Whether you’re working on a prototype, a medical component, or a low-volume industrial part, these principles hold true.
Ready to bring cost-efficient precision to your next project? Work with a trusted CNC machining service that provides design support and fast turnaround to help you succeed.