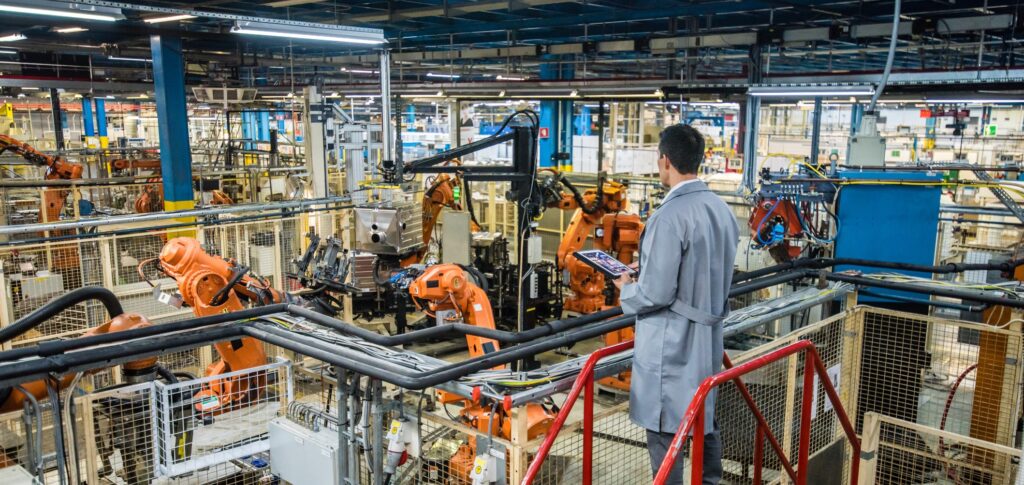
assembly line production
Let’s be honest — manufacturing today is all about speed, precision, and efficiency. And nothing embodies those goals more than automation. If your production line still relies on manual labor for repetitive tasks, you’re probably falling behind. Automation in assembly line production isn’t just the future — it’s the now. It’s time to understand how it works and what it means for your operations.
Curious about how automation can supercharge your efficiency? You might want to check out Assembly Line Production to see what expert services are available to help you modernize.
1. What is Automation in Assembly Line Production?
Simply put, automation in assembly lines means using machines, control systems, and information technologies to carry out production tasks — with minimal human intervention. It includes everything from robotic arms that screw in bolts to software that manages production flow.
This kind of automation isn’t limited to huge corporations anymore. Businesses of all sizes are now adopting it to reduce costs, improve quality, and stay competitive.
2. The Evolution of the Assembly Line
To understand where we’re going, it helps to know where we’ve been. Assembly lines have come a long way since Henry Ford first introduced them in the early 1900s. Back then, they were all about manual processes and task specialization.
Fast forward to today, and we’ve got fully automated lines that run 24/7 with incredible precision — and without a single human hand touching the product. That’s a massive leap in both capability and efficiency.
3. Types of Automation Used in Assembly Lines
Not all automation is created equal. Here are the most common types used in production environments:
-
Fixed automation: Best for high-volume, repeat production tasks. Think automotive lines.
-
Programmable automation: Allows reprogramming for different products, ideal for batch production.
-
Flexible automation: Quickly adaptable for product changes, offering the most versatility.
Choosing the right type depends on your production goals, product variety, and budget.
4. Benefits of Automating Your Assembly Line
There’s a reason automation is booming. The benefits speak for themselves:
-
Higher throughput: Machines don’t need breaks.
-
Improved accuracy: Eliminate human error.
-
Lower operating costs: Fewer workers needed for repetitive tasks.
-
Better quality control: Consistency is key.
-
Faster ROI: Automation systems often pay for themselves quickly through cost savings.
If you’re still relying on manual processes, you’re likely leaving money on the table.
5. Common Applications Across Industries
Automation is used in just about every industry you can think of — not just cars and electronics. You’ll find it in:
-
Food and beverage packaging
-
Consumer electronics assembly
-
Pharmaceutical production
-
Aerospace component manufacturing
-
Medical device fabrication
Each industry uses a tailored approach to automation depending on regulations, product design, and customer demand.
6. Key Technologies Powering Automation
Automation systems today are smarter and more connected than ever before. Some of the core technologies include:
-
Robotics: From simple pick-and-place to complex multi-axis operations
-
Sensors and vision systems: For defect detection and real-time adjustments
-
PLC (Programmable Logic Controllers): The brains behind machine control
-
HMI (Human Machine Interface): For monitoring and interacting with systems
-
IoT integration: Enables remote tracking and performance analysis
These technologies combine to form efficient, intelligent production environments.
7. How Automation Enhances Workplace Safety
It’s not just about speed and accuracy. Automation also makes the factory floor safer. Machines can handle dangerous, repetitive, or high-precision tasks that could otherwise injure workers.
In fact, integrating automation often leads to a noticeable drop in workplace accidents and fatigue-related errors. That’s a win for both productivity and employee well-being.
8. Real-Time Monitoring and Data Collection
Today’s automated lines don’t just perform tasks — they think, track, and report. Through sensors and IoT-enabled tools, manufacturers can monitor everything in real time: production speed, energy usage, maintenance needs, and quality metrics.
This data helps businesses make informed decisions quickly, whether it’s optimizing production schedules or fixing potential issues before they cause downtime.
If you want to explore how real-time data can optimize your operation, this guide on assembly line production is a great place to start.
9. Preparing Your Facility for Automation
Thinking about making the switch? Start by evaluating your current setup. Ask yourself:
-
What processes are repetitive or prone to error?
-
What’s your current production capacity?
-
How flexible is your current equipment?
Next, work with an automation expert to plan a solution that fits your goals and budget. Sometimes, even small upgrades like a robotic arm or automated conveyor can deliver major results.
10. The Future of Assembly Line Automation
What’s next in this space? Expect more integration with AI and machine learning. We’re heading toward factories that optimize themselves, predict failures before they happen, and adjust workflows without human input.
As costs continue to drop and systems become more user-friendly, automation will become a standard — not a luxury — across industries.
Final Thoughts
Automation in assembly line production isn’t just a trend — it’s the foundation of modern manufacturing. It boosts speed, improves safety, cuts costs, and empowers businesses to scale like never before.
Whether you’re just starting out or ready to expand, embracing automation is one of the smartest moves you can make in today’s fast-paced market. Don’t get left behind — invest in the tools that will carry your production line into the future.