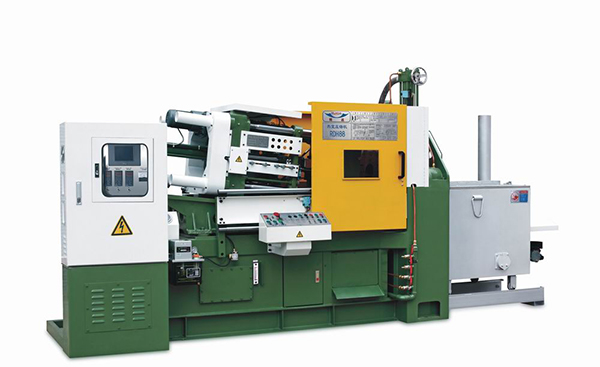
aluminum die casting
In today’s fast-paced manufacturing world, consistency, accuracy, and strength are non-negotiables. Whether it’s automotive parts, aerospace components, or intricate machinery housings, industries demand high-performance materials and efficient production techniques. Among the most reliable and scalable solutions is aluminum die casting, a cornerstone method for creating complex metal parts with precision and durability.
But what is die casting, and why has aluminum die casting become a go-to choice for manufacturers globally?
What is Die Casting?
At its core, die casting is a metal casting process where molten metal is forced into a mold cavity under high pressure. These molds, also known as dies, are made of hardened tool steel and are designed to be highly precise and reusable. The goal is simple: produce large volumes of metal parts with consistent shape, surface finish, and integrity.
This method is ideal for mass-producing components where quality can’t be compromised. From car engines to laptop frames, die casting ensures uniformity without sacrificing performance.
Why Aluminum?
While various metals like zinc, magnesium, and copper can be used in this process, aluminum die casting stands out for several reasons:
-
Lightweight but Strong: Aluminum is incredibly light compared to other metals, yet it retains structural strength. This makes it a top choice in automotive and aerospace industries where weight reduction is critical.
-
Corrosion Resistance: Aluminum offers natural resistance to corrosion, increasing the lifespan of parts and reducing maintenance costs.
-
Thermal Conductivity: Excellent thermal conductivity allows for better heat dissipation, which is especially useful in electronic enclosures or engine parts.
-
Recyclability: Aluminum can be recycled without losing its properties, making aluminum die casting an eco-friendly option for sustainable production.
The Process of Aluminum Die Casting
There are two primary types of aluminum die casting processes: hot chamber and cold chamber. For aluminum, the cold chamber method is more common due to the metal’s high melting point.
Here’s a step-by-step breakdown:
-
Die Preparation: The mold is cleaned and lubricated to ensure smooth release of the cast part.
-
Injection: Molten aluminum is poured into the injection chamber and forced into the die using a piston.
-
Cooling: The metal solidifies quickly inside the die.
-
Ejection: Once cooled, the part is ejected from the die.
-
Trimming: Excess material (known as flash) is removed, and the part is polished or machined as needed.
Each step is engineered to optimize speed, accuracy, and efficiency.
Benefits of Aluminum Die Casting for Manufacturers
Across industries, aluminum die casting delivers clear advantages that drive productivity and quality.
-
Speed: The automated process allows rapid production of thousands of parts in short timeframes.
-
Accuracy: Tight tolerances ensure minimal deviation, often eliminating the need for secondary machining.
-
Surface Finish: The resulting components have smooth surfaces, ideal for plating, painting, or powder coating.
-
Cost-Effective: Especially in high-volume production, the cost per unit drops significantly.
In sectors like electronics, healthcare, defense, and consumer goods, these benefits turn into competitive advantages.
Exploring the Aluminum Casting Die
An essential component of the aluminum die casting process is the aluminum casting die itself. These are custom-engineered molds that determine the shape, dimensions, and surface texture of the final product. High-quality dies are precision-machined using advanced tools and must withstand extreme pressure and temperature.
The life expectancy of an aluminum casting die depends on several factors including the complexity of the part, the temperature of the molten metal, and the frequency of use. However, with proper care and maintenance, a die can produce hundreds of thousands of parts before needing replacement.
Common Applications of Aluminum Die Casting
The use of aluminum die casting stretches far beyond one industry. It’s a versatile process that supports innovation in:
-
Automotive: Engine blocks, transmission housings, wheels, and more.
-
Aerospace: Lightweight structures and internal components.
-
Consumer Electronics: Laptop bodies, camera housings, and speaker frames.
-
Industrial Equipment: Pumps, compressors, and motor casings.
-
Lighting Industry: Heat sinks and frames for LED lighting.
Wherever a strong, lightweight, and corrosion-resistant part is needed, aluminum die casting finds its place.
Why Choose the Right Partner?
Though the process may sound standardized, the reality is far more complex. Success in aluminum die casting hinges on working with a manufacturing partner who understands not just the science, but also the art of casting.
A great partner:
-
Uses advanced simulation tools to predict and prevent defects.
-
Offers in-house tooling and mold maintenance.
-
Maintains strict quality control throughout the production cycle.
-
Has deep experience across a wide range of industries.
That’s where trusted manufacturers like Zintilon come into play. While we rarely mention our name, the focus remains on quality, reliability, and tailored solutions for businesses of all sizes.
Sustainability in Die Casting
Another reason aluminum die casting is gaining traction is its environmental footprint. Aluminum is among the most recyclable materials on the planet. By using secondary (recycled) aluminum and optimizing energy use in the production line, manufacturers can drastically reduce carbon emissions.
Additionally, the accuracy of the casting process reduces material waste, which means fewer raw resources are consumed. It’s a win-win for businesses and the environment.
Challenges in Aluminum Die Casting
No process is without its hurdles. Here are a few challenges commonly faced:
-
Porosity: Trapped air or gas can cause internal holes, affecting strength.
-
Thermal Stress: Repeated heating and cooling may weaken dies over time.
-
Design Complexity: Extremely intricate parts may require multiple dies or secondary machining.
Fortunately, with modern software simulations and experienced engineers, these issues can be predicted, minimized, or entirely avoided.
Future Trends in Aluminum Die Casting
The world of aluminum die casting continues to evolve with advancements in:
-
3D Printed Dies: Faster prototyping and shorter lead times.
-
AI & Automation: Smart factories improve process control and reduce defects.
-
Alloy Development: Stronger, more heat-resistant aluminum alloys.
-
Green Casting: Solar-powered casting lines and zero-waste initiatives.
With innovation at its core, the future of aluminum die casting looks bright and sustainable.
Conclusion
From everyday gadgets to high-stakes aerospace components, aluminum die casting remains an indispensable technique in modern manufacturing. Its unbeatable combination of strength, precision, and efficiency makes it the backbone of countless industries worldwide.
Whether you’re new to the process or a seasoned engineer, one thing is clear: understanding and leveraging aluminum die casting is no longer optional—it’s essential. And with the right partner and tools, the possibilities are endless.