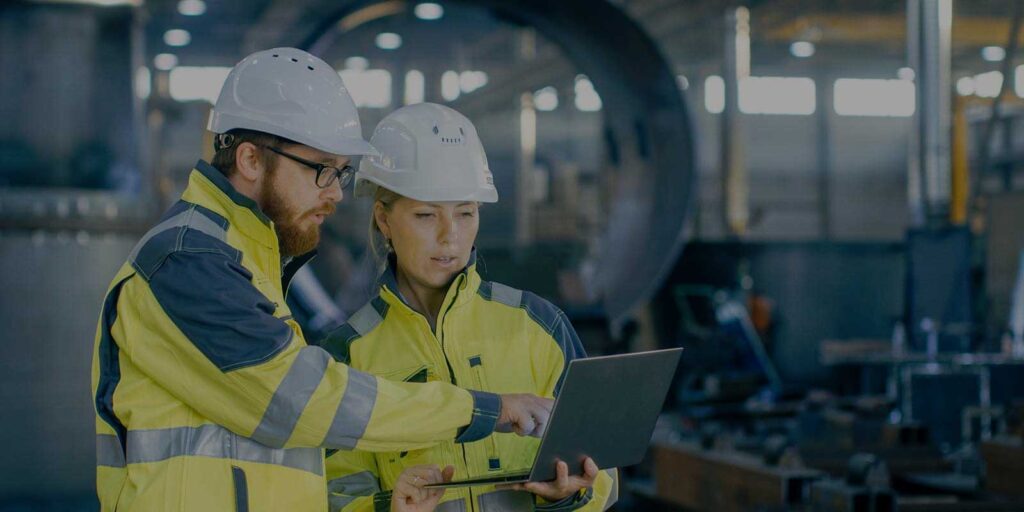
In today’s fast-paced manufacturing landscape, the need for improved efficiency and streamlined operations is greater than ever. Custom manufacturing software offers tailored solutions to meet the unique requirements of individual manufacturers. It simplifies the complexity of production processes, allowing businesses to improve their workflows, reduce costs, and enhance overall productivity. Let’s explore how custom manufacturing software can significantly improve production efficiency across various industries.
Streamlining Production Planning and Scheduling
One of the key areas where custom manufacturing software excels is in production planning and scheduling. Traditional methods of scheduling often result in bottlenecks, delays, and poor resource utilization. Custom software provides real-time data and powerful algorithms to optimize production schedules, taking into account variables like inventory levels, machine capacity, and labor availability. This results in more accurate production timelines, ensuring products are delivered on time without sacrificing quality.
Manufacturers can also automate routine tasks such as order tracking, material allocation, and job prioritization. This automation reduces manual input, eliminates errors, and accelerates decision-making. By having a clear view of the entire production pipeline, manufacturers can adjust quickly to changes in demand, machine downtimes, or supply chain disruptions.
Inventory Management Made Simple
Inventory management is another critical aspect of production efficiency. Keeping track of raw materials, parts, and finished products can become increasingly difficult as manufacturing operations grow. Custom manufacturing software can provide a centralized platform for real-time inventory tracking. By integrating with other systems, such as accounting or procurement, manufacturers can automatically reorder stock when it runs low, ensuring they never run out of essential materials.
With a cloud-based solution, the software can continuously update inventory levels and provide predictive analytics to help manufacturers plan for future demand. This reduces the risk of overstocking or understocking, both of which can lead to lost revenue and increased operational costs. As a result, manufacturers can maintain optimal inventory levels, avoid production delays, and minimize wastage.
Enhanced Data Collection and Analytics
Another major benefit of custom manufacturing software is its ability to collect and analyze vast amounts of production data. In the past, manufacturers often relied on manual record-keeping, which could lead to inconsistencies and errors. With modern software, data is automatically collected from machines, sensors, and workstations in real-time. This data can then be analyzed to identify inefficiencies, predict equipment failures, and optimize workflows.
The software also allows manufacturers to track key performance indicators (KPIs) such as production speed, equipment utilization, and quality control. By having access to accurate and up-to-date data, manufacturers can make data-driven decisions to improve production processes. This level of insight would be difficult to achieve with traditional methods of tracking and reporting, making custom software an indispensable tool for enhancing efficiency.
Cloud-Based Manufacturing Software
One of the most significant innovations in recent years has been the rise of cloud based manufacturing software. Unlike traditional on-premise software, cloud solutions provide greater flexibility, scalability, and accessibility. Cloud-based software allows manufacturers to access their systems from any device with an internet connection, making it easier to manage production remotely or across multiple sites.
In addition to improving accessibility, cloud-based solutions reduce the need for costly hardware and IT infrastructure. Manufacturers can rely on the software provider to handle updates, backups, and security, reducing the burden on internal IT teams. With the ability to scale resources up or down as needed, cloud-based manufacturing software is ideal for businesses that experience fluctuations in demand or have multiple locations.
By integrating cloud-based systems with other software tools, manufacturers can create a seamless ecosystem that provides real-time insights into every aspect of their operations. This interconnectedness allows for more informed decision-making and greater efficiency throughout the entire production process.
Improving Quality Control
Ensuring consistent product quality is essential for any manufacturing operation. Custom manufacturing software provides robust quality control features that can help businesses maintain high standards. The software allows manufacturers to implement automated inspections, monitor production tolerances, and track defect rates in real-time.
Custom software can be integrated with IoT devices and sensors to monitor various aspects of the production process, such as temperature, pressure, and material quality. If any parameter falls outside of the acceptable range, the system can automatically halt production or alert operators to take corrective action. This proactive approach to quality control ensures that issues are addressed before they escalate, reducing the risk of defective products and costly rework.
Facilitating Collaboration and Communication
Collaboration and communication between departments are vital for smooth production operations. Custom manufacturing software serves as a centralized platform for team members across different departments—such as production, procurement, and sales—to communicate in real-time. This transparency improves decision-making and ensures everyone is aligned with production goals.
Moreover, when integrated with customer relationship management (CRM) and enterprise resource planning (ERP) systems, manufacturers can better align production schedules with customer orders and market demand. This integrated communication helps prevent stockouts, delays, or overproduction, ultimately improving customer satisfaction and production efficiency.
Reducing Operational Costs
In an increasingly competitive market, manufacturers must continually look for ways to reduce costs without sacrificing quality. Custom manufacturing software can help businesses identify areas where cost savings are possible. By automating processes, reducing waste, improving inventory management, and optimizing machine usage, manufacturers can cut operational costs while improving efficiency.
For example, custom software can identify underutilized equipment and suggest adjustments to the production schedule. It can also analyze labor costs and recommend ways to improve workforce productivity. These insights help manufacturers make smarter financial decisions and allocate resources more effectively.
Conclusion
Custom manufacturing software is a powerful tool that enhances production efficiency by automating tasks, improving data collection, and providing real-time insights. With the rise of cloud-based solutions, manufacturers can access their systems from anywhere, scale operations easily, and reduce the need for on-premise infrastructure. From better inventory management to improved quality control, custom manufacturing software plays a crucial role in streamlining operations and helping manufacturers stay competitive in an increasingly complex market.
By implementing custom software tailored to their specific needs, manufacturers can ensure they are operating at peak efficiency, delivering high-quality products, and meeting customer expectations. The future of manufacturing is digital, and custom software is at the forefront of this transformation.