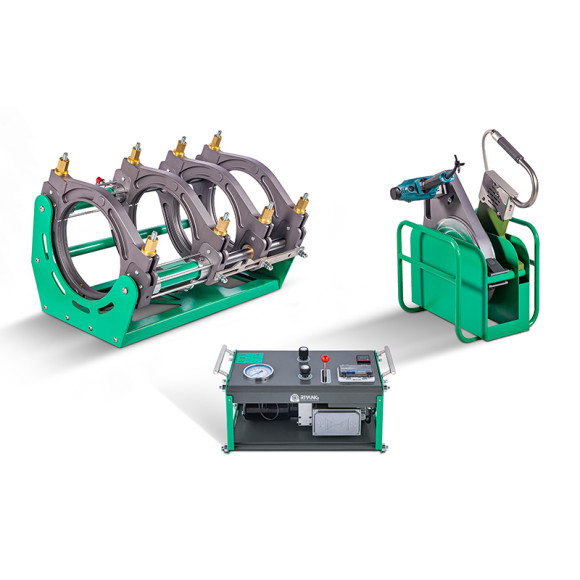
As infrastructure needs grow across industries such as construction, water management, and energy, the demand for durable and reliable piping solutions intensifies. High-Density Polyethylene (HDPE) piping systems are increasingly becoming the backbone of modern piping networks. Known for their flexibility, corrosion resistance, and cost-efficiency, HDPE pipes are well-suited for projects ranging from urban water supply to oil and gas transportation. However, the true strength of any HDPE system lies in the quality of its joints. In large-scale or high-pressure applications, even a minor leak can escalate into a significant problem—costly and difficult to fix. That’s where the role of a hydraulic butt fusion machine becomes critical.
Understanding the Technology Behind Hydraulic Butt Fusion
Butt fusion welding is the most widely used technique for joining HDPE pipes. It involves heating two pipe ends, pressing them together, and allowing them to cool under pressure to create a seamless, monolithic joint. This joint is as strong as—or stronger than—the original pipe itself. Among the different types of fusion methods, hydraulic butt fusion stands out for its speed, accuracy, and ability to handle high-volume, high-diameter pipes.
In this process, the hydraulic system applies consistent pressure throughout the welding cycle. Unlike manual machines that rely heavily on operator skill, a hydraulic unit ensures uniform heating and fusion with minimal human error. The entire cycle—clamping, facing, heating, and joining—is driven by hydraulic power. This makes the system especially effective for heavy-duty or field applications where precision and repeatability are paramount.
By leveraging advanced pressure control and automated cycles, a hydraulic butt fusion machine ensures consistent weld quality across varying site conditions. This is particularly valuable for contractors working in regions with challenging terrains or extreme climates, where stable and strong pipe joints are essential for operational reliability.
Why Choose Hydraulic Butt Fusion for Demanding Projects?
Infrastructure projects face different stressors depending on geography, usage, and environmental conditions. For instance, mining sites deal with high-pressure slurry systems, while desert pipeline installations face extreme temperature fluctuations. In both cases, HDPE pipes are a popular choice due to their durability and resilience. However, these projects also demand robust joining methods that can meet performance expectations under pressure.
Hydraulic butt fusion delivers multiple advantages:
1. Superior Joint Strength and Reliability
Because the fusion process creates a homogenous joint without additional materials, there are no weak points. The welded area becomes part of the pipe, effectively eliminating risks associated with leaks or joint failure. This is particularly important in underground and submerged installations where access for repair is limited or impossible.
2. Consistent Welding Quality
Hydraulic systems enable precise control of key welding parameters like temperature, pressure, and alignment. Built-in timers and sensors help maintain consistent heating and joining cycles, reducing the likelihood of operator-induced errors. The result is high-quality, repeatable welds across the entire pipeline.
3. Adaptability Across Pipe Sizes and Materials
Most hydraulic fusion machines can handle a wide range of pipe diameters, making them suitable for various project scopes. From small utility lines to large water mains or industrial pipelines, the same equipment can be used with minor adjustments. In addition, many models are compatible with different types of polyethylene such as PE100, PE80, and PE63.
4. Enhanced Productivity and Reduced Labor Costs
Time is a critical factor on construction sites. Hydraulic fusion equipment significantly speeds up the welding process compared to manual techniques. Fewer weld defects also mean fewer do-overs, reducing project delays. Additionally, with simplified controls, even moderately trained operators can achieve professional-grade welds.
5. Safety and Environmental Compliance
Hydraulic fusion processes do not involve open flames or hazardous chemicals, making them safer for operators and environmentally friendly. This aligns with global trends toward green construction practices and helps contractors comply with international safety standards.
Key Features to Look for in a Hydraulic Butt Fusion Machine
Not all fusion machines are created equal. When investing in hydraulic equipment for HDPE welding, it’s essential to evaluate the machine’s specifications and features in relation to the project requirements.
– Pressure Control Systems
Look for systems with digital or mechanical pressure regulators that maintain consistent force throughout the welding cycle. This ensures proper fusion without damaging the pipe ends.
– Temperature Regulation
The heating plate should offer stable and uniform temperature distribution. Some machines feature integrated thermostats or PID controllers to prevent overheating or underheating, which can compromise weld strength.
– Strong Clamping and Alignment Mechanism
Pipe misalignment is a common cause of weld failure. A good hydraulic machine offers rigid clamps and precise alignment guides to keep pipe ends perfectly in place during fusion.
– Durability and Portability
Projects in remote areas require equipment that’s easy to transport and resilient to dust, moisture, and rough handling. Machines with compact frames, protective cases, and weather-resistant components offer better long-term value.
– Compliance with International Standards
Always verify whether the machine complies with ISO 21307 or DVS 2207 welding standards. Compliance assures that the machine produces joints that meet global benchmarks for safety and durability.
Real-World Applications in Demanding Sectors
The use of hydraulic butt fusion technology is widespread across sectors where pipe performance cannot be compromised:
-
Water Supply and Irrigation: Municipal water networks benefit from leak-free distribution over long distances, minimizing maintenance needs.
-
Oil and Gas Pipelines: In high-pressure and corrosive environments, a seamless joint reduces failure risks.
-
Mining and Slurry Systems: Hydraulic fusion handles abrasive materials and pressure surges with ease.
-
Industrial Processing Plants: Chemicals, wastewater, and other fluids require secure containment—something HDPE welded with precision can provide.
-
Renewable Energy: Solar farms and wind energy plants often use underground piping networks that must remain maintenance-free for decades.
Conclusion
In high-stakes environments, the strength and reliability of pipeline joints are non-negotiable. As HDPE continues to replace traditional materials like steel and concrete in infrastructure projects, the need for high-performance welding technologies becomes even more urgent. A hydraulic butt fusion machine offers the precision, speed, and reliability necessary to meet the demands of modern construction and industrial operations.
By investing in quality fusion equipment, contractors and engineers not only ensure the success of current projects but also future-proof their infrastructure against failures. Whether you’re installing a water distribution system in a dense urban area or laying pipelines across harsh terrain, hydraulic butt fusion is a smart, sustainable, and technically superior solution for HDPE piping systems.