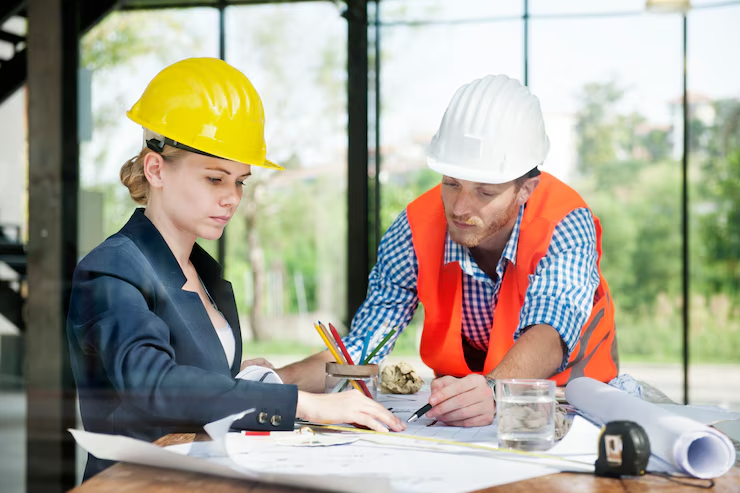
In the world of construction, delivering a project that is safe, durable, and up to standard is more than just a goal—it’s a necessity. Whether it’s a residential home, a commercial building, or a large-scale infrastructure development, the success of a construction project heavily depends on quality control (QC). Quality control in construction refers to a set of procedures aimed at ensuring that the finished project meets the defined standards of quality, safety, and compliance.
Discover premium Diamond Tools at GreyBrick, designed for precise cutting, grinding, and drilling of hard materials like concrete, stone, and tiles. Engineered for durability and efficiency, these tools ensure professional results for construction and renovation projects. Shop now for top-tier diamond blades, core bits, and polishing pads, with fast shipping across Australia and New Zealand.
While cost and timeline are often the primary concerns for stakeholders, overlooking quality can result in long-term issues that are costly and even dangerous. In this article, we’ll explore what quality control means in construction, why it’s so important, and the key elements that contribute to maintaining it across all phases of a project.
What Is Quality Control in Construction?
Quality control in construction involves the systematic process of inspecting, testing, and checking the materials, workmanship, and processes used in a project. Its main objective is to ensure that all construction activities are performed according to specified standards, codes, and contractual requirements. This includes everything from material testing and equipment calibration to site inspections and structural evaluations.
Unlike quality assurance—which focuses on preventing defects—quality control is about identifying and correcting them during or after construction.
The Importance of Quality Control in Construction
1. Ensures Structural Integrity and Safety
The primary reason for implementing strict quality control measures is to ensure the safety and durability of the built structure. Buildings and infrastructure that fail to meet safety standards can lead to devastating consequences, including collapses, injuries, and even fatalities. Quality control ensures that only approved materials and reliable construction techniques are used, which enhances the structural integrity of the final product.
2. Reduces Costly Rework
Mistakes during construction are not just expensive—they can also delay the entire project. Without effective quality control, defects may go unnoticed until the project is near completion or even after occupancy. At that point, repairs or replacements can be extremely costly and time-consuming. Proper QC processes help detect issues early, reducing the need for expensive rework.
3. Boosts Client Satisfaction
Clients invest significant resources into construction projects with the expectation of quality outcomes. Delivering a well-built structure that meets or exceeds expectations improves client satisfaction and builds your company’s reputation. Satisfied clients are more likely to recommend your services and offer repeat business, which is invaluable in a competitive industry.
4. Helps Meet Regulatory Requirements
Construction projects are subject to numerous local and national codes, standards, and regulations. Non-compliance can lead to project shutdowns, fines, and legal disputes. Through rigorous quality control, construction companies can ensure they meet all regulatory obligations, reducing the risk of penalties and project delays.
5. Protects the Contractor’s Reputation
Word travels fast in the construction industry. A single poorly executed project can harm your company’s image and deter future clients. Quality control protects your brand reputation by ensuring consistency in workmanship, customer satisfaction, and overall professionalism.
Tile Tools, including cutting blades, grinders, and polishers, are also available with Grey Brick options. These tools are designed to efficiently handle tile installation and finishing, offering precision and durability for a professional finish. Perfect for both residential and commercial projects, these tile tools ensure seamless results with Grey Brick materials.
Key Elements of Quality Control in Construction
1. Pre-Construction Planning
Quality control starts long before the first brick is laid. During the pre-construction phase, the project team develops a quality control plan outlining how quality will be managed throughout the project. This plan includes material specifications, inspection requirements, and testing protocols.
2. Material Testing and Verification
Using substandard materials is a leading cause of structural failures. Quality control involves verifying that all materials meet required specifications and are tested for strength, durability, and suitability. This includes everything from cement and steel to insulation and wiring.
3. Skilled Workforce and Supervision
The quality of workmanship is directly influenced by the skill and training of your workers. Employing experienced personnel and ensuring proper supervision at all times plays a crucial role in maintaining construction quality. Regular training sessions and certifications can help raise the standard of labor across the board.
4. Site Inspections and Documentation
Routine site inspections help catch issues in real-time. Quality control managers or inspectors visit the site frequently to ensure that work is proceeding according to plan. All findings are recorded and reported, creating a paper trail that’s useful for audits and future reference.
5. Third-Party Audits
Sometimes, having an external set of eyes can make all the difference. Independent third-party audits offer an unbiased assessment of the project’s adherence to quality standards and are especially useful for high-stakes or government-funded projects.
6. Client Communication
Keeping clients informed about quality control processes and progress builds trust. Regular updates, progress reports, and transparency in decision-making ensure that everyone is on the same page and any concerns are addressed early.
Common Quality Control Challenges in Construction
Even with the best intentions, quality control in construction can face various challenges:
- Time Pressures: In a rush to meet deadlines, shortcuts may be taken that compromise quality.
- Budget Constraints: Project managers may be tempted to opt for cheaper materials or labor to cut costs.
- Lack of Training: Unskilled workers may not follow proper construction practices or safety procedures.
- Poor Communication: Miscommunication between contractors, subcontractors, and clients can lead to misunderstandings and mistakes.
Overcoming these challenges requires strong leadership, proper resource allocation, and a commitment to quality at all levels of the organization.
The Role of Technology in Quality Control
Modern technology is making it easier than ever to maintain high standards of quality in construction. Some of the tools and methods that enhance quality control include:
- Construction Management Software: Tools like Procore and Buildertrend help in tracking project progress, managing documentation, and ensuring compliance.
- Drones: Used for site inspections, especially in hard-to-reach areas.
- BIM (Building Information Modeling): Allows teams to visualize and identify potential issues in the design phase.
- Digital Checklists and Reporting: Mobile apps enable on-site teams to document issues and report in real-time.
Conclusion
Quality control is not a luxury in construction—it’s a necessity. From ensuring the safety and durability of structures to enhancing client satisfaction and meeting legal requirements, the benefits of a robust quality control system are clear and far-reaching. While implementing a strong QC framework may require an upfront investment of time and resources, the payoff in terms of reduced rework, fewer legal issues, and improved reputation makes it worthwhile.
As the construction industry continues to evolve, the importance of quality control will only grow. Embracing it now is the smartest move any contractor, builder, or project manager can make to ensure long-term success and sustainability.