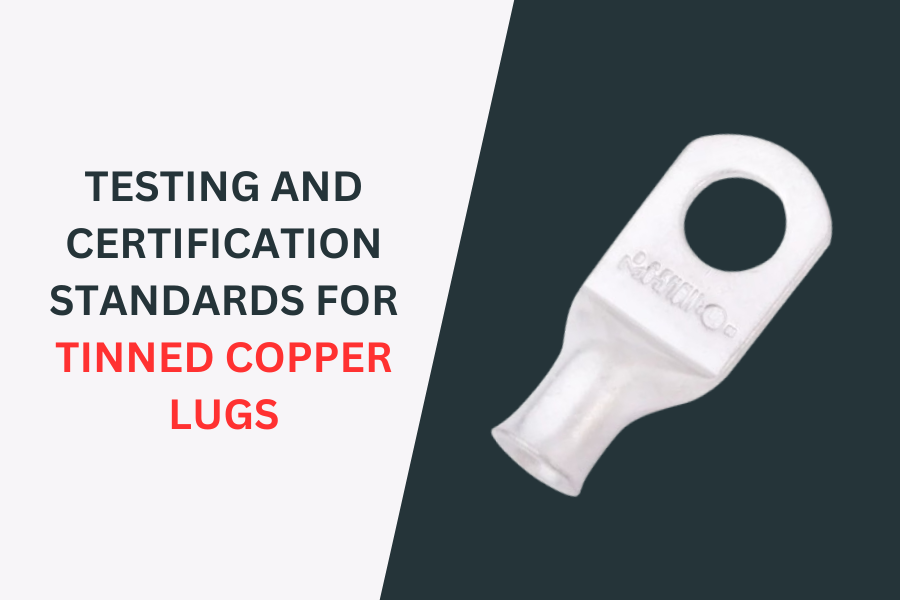
Tinned copper lugs are essential components in electrical installations, ensuring safe and efficient connections between wires and electrical equipment. These lugs are crafted from copper and coated with a thin layer of tin to protect against corrosion, ensuring longevity and reliability in various environmental conditions. For these lugs to perform effectively and meet safety and quality requirements, they must undergo rigorous testing and adhere to specific certification standards. This blog will explore the various testing and certification standards for tinned copper lugs, highlighting their importance in the electrical industry.
What Are Tinned Copper Lugs?
Tinned copper lugs are connectors used in electrical circuits to terminate cables and wires, typically providing a stable and secure electrical connection. The tin coating is applied to the copper material to prevent corrosion, enhance the lug’s durability, and ensure that it withstands exposure to environmental factors such as moisture, extreme temperatures, and corrosive substances. These lugs are commonly used in a wide range of industries, including power generation, electrical transmission, automotive, and telecommunications.
Importance of Testing and Certification for Tinned Copper Lugs
Testing and certification standards are crucial to guarantee the safety, performance, and reliability of tinned copper lugs in electrical installations. Electrical systems are highly sensitive, and poor-quality components can lead to failures, which may result in equipment damage, system downtime, and, in some cases, dangerous incidents like fires or electrical shocks. Thus, manufacturers and users must adhere to strict testing protocols and ensure compliance with industry certifications.
Certification provides assurance that the product has undergone thorough testing and meets the necessary safety and quality standards. It is important for both manufacturers and consumers to understand these standards and ensure that they are using compliant, certified products in their electrical systems.
Key Testing Standards for Tinned Copper Lugs
Several testing methods and standards are applied to tinned copper lugs to assess their performance, durability, and safety. These tests are designed to simulate real-world conditions, ensuring that the lugs can perform as expected under various circumstances. Some of the key testing standards for tinned copper lugs include:
1. Electrical Conductivity Testing
Electrical conductivity is one of the primary characteristics of tinned copper lugs, as their main function is to facilitate the transmission of electricity. Copper, known for its excellent conductivity, is the material of choice for most lugs, but the tin coating can influence conductivity.
Testing involves measuring the electrical resistance of the lug to ensure it allows efficient current flow. If the tin coating is too thick or uneven, it may impact the overall conductivity, leading to potential overheating or energy losses. Compliance with international standards like the ASTM B193-16, which specifies the electrical conductivity of copper and its alloys, ensures that tinned copper lugs meet the necessary requirements for electrical performance.
2. Tensile Strength and Mechanical Testing
Tinned copper lugs must be able to withstand mechanical stresses, including pulling, bending, and twisting forces, during installation and operation. The tensile strength of the copper material and the integrity of the tin coating are critical to ensure that the lug can endure without deformation or failure.
Mechanical testing involves subjecting the lugs to various stress tests to determine their breaking point, elongation, and ability to maintain a secure connection under mechanical strain. This testing typically adheres to standards such as the IEC 61238-1:2003, which outlines the mechanical and electrical testing of compression terminals and splices, ensuring that the lugs meet the necessary mechanical strength requirements.
3. Corrosion Resistance Testing
Corrosion resistance is one of the main reasons for choosing tinned copper lugs over pure copper lugs. The tin coating acts as a protective layer to prevent oxidation and corrosion, which could weaken the lug and compromise its performance. Corrosion resistance testing simulates various environmental conditions, such as exposure to humidity, saltwater, and acidic or alkaline substances, to assess the ability of the tin coating to protect the copper beneath.
The most common test for corrosion resistance is the salt spray test, which subjects the lugs to a salt mist environment for extended periods. The result indicates how well the lug resists corrosion over time. Standards like ASTM B117-19, which specifies the practice for operating salt spray (fog) apparatus, are widely used to evaluate the corrosion resistance of tinned copper lugs.
4. Temperature Cycling and Thermal Stability Testing
Electrical systems often experience temperature fluctuations, particularly in outdoor or industrial environments. Tinned copper lugs must be able to withstand high temperatures during operation and not degrade under thermal cycling. Thermal stability testing involves exposing the lugs to extreme temperature cycles, ranging from freezing conditions to high-heat environments, to assess the material’s ability to maintain its integrity.
These tests help determine the durability of the tin coating and ensure that the lugs will not crack, degrade, or lose conductivity over time. The results are in line with standards such as IEC 60068-2-1, which provides guidance for environmental testing, including temperature cycling and exposure.
Certification Standards for Tinned Copper Lugs
In addition to testing, tinned copper lugs must meet specific certification standards to demonstrate their compliance with safety and quality requirements. These certifications are recognized by regulatory bodies, industry groups, and consumers worldwide, ensuring that the products meet the highest performance criteria.
1. UL Certification (Underwriters Laboratories)
The UL mark is one of the most recognized certification standards in the electrical industry. UL certifies that the product complies with specific safety and performance standards, including those for electrical conductivity, mechanical strength, and fire resistance. Tinned copper cable lugs that are UL-certified meet the necessary requirements for use in electrical systems, ensuring their reliability and safety.
2. CE Marking (Conformité Européene)
The CE mark indicates that a product meets the safety and performance requirements of the European Union. Tinned copper lugs that bear the CE marking are compliant with EU regulations, including those related to electrical safety, environmental impact, and material quality.
3. ISO Certification (International Organization for Standardization)
ISO certification is another important mark of quality, ensuring that the manufacturing processes and quality control measures meet international standards. ISO 9001, for example, sets requirements for quality management systems and is often applied to manufacturers of tinned copper lugs to guarantee consistency and reliability in production.
Conclusion
Testing and certification standards for tinned copper cable lugs play an essential role in ensuring the safety, reliability, and performance of electrical connections. Rigorous testing methods assess the lugs’ conductivity, mechanical strength, corrosion resistance, and thermal stability, while certification marks such as UL, CE, and ISO offer assurance that the product complies with relevant standards. Adhering to these testing and certification protocols helps prevent failures, increases the lifespan of electrical systems, and ensures the safety of both the