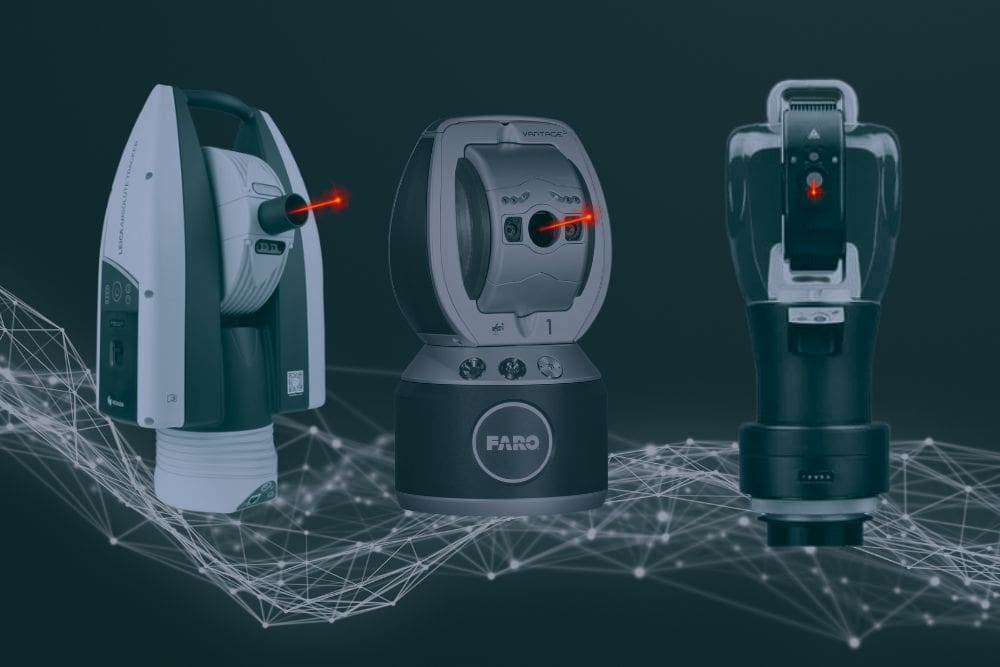
Laser Tracking Systems
In today’s fast-paced manufacturing environment, ensuring precision and consistency is more important than ever. That’s where laser tracking systems come in. These advanced tools have revolutionized the way industries handle quality control, offering unparalleled accuracy and efficiency.
Laser trackers are not just for measuring; they provide real-time, high-precision data that helps businesses streamline processes, reduce errors, and maintain high-quality standards. If you’re looking to learn how Laser Tracking Systems can improve your quality control processes, you’ve come to the right place.
What Is a Laser Tracking System?
A laser tracking system is a 3D measurement tool used to measure the position and movement of objects in real-time. It operates by emitting a laser beam towards a target and then calculating the distance and angle of the returned laser signal. This data is then processed to determine the exact position in three-dimensional space.
These systems are commonly used in large-scale industrial applications such as aerospace, automotive, construction, and heavy machinery, where high precision is crucial. Unlike traditional measuring methods, laser trackers are incredibly accurate, offering measurements to the micron level, making them ideal for quality control in manufacturing processes.
Why Laser Tracking Systems Matter for Quality Control
Quality control is an essential part of any manufacturing operation. Without proper measurement tools, it’s easy to overlook even the smallest defects, which can lead to costly repairs or even product recalls. This is where laser tracking systems provide significant advantages.
Laser tracking systems allow for quick, real-time measurements across large surfaces or components, ensuring every part meets the required specifications. They’re particularly useful in applications that involve intricate designs or complex geometries, which traditional measurement tools struggle to handle.
Key Benefits of Laser Tracking Systems in Quality Control
1. High Accuracy and Precision
One of the main reasons why laser tracking systems are so valuable in quality control is their accuracy. These systems offer precision that goes beyond traditional tools, allowing manufacturers to detect even the smallest deviations from specified dimensions. This level of accuracy is vital in industries like aerospace and automotive manufacturing, where a tiny mistake can lead to significant performance issues.
2. Real-Time Measurements
Unlike traditional inspection methods that require multiple steps, laser trackers can measure and provide real-time feedback on the quality of the product. This immediate data allows for quicker decision-making, enabling teams to make adjustments during the manufacturing process rather than after the fact.
3. Non-Contact Measurement
Laser trackers are non-contact measurement tools, which means they don’t physically touch the object being measured. This feature is especially beneficial when measuring delicate or sensitive parts that could be damaged by contact-based measuring instruments. Non-contact measurement reduces the risk of errors caused by tool wear and tear.
4. Efficiency and Speed
Laser tracking systems can measure large surfaces and complex geometries much faster than traditional methods. This speed is critical for high-volume production environments, where efficiency and throughput are key factors in meeting deadlines and customer demands.
How Laser Tracking Systems Integrate with Quality Control Processes
Laser tracking systems play a central role in modern quality control systems. Here’s how they fit into the process:
1. In-Process Inspection
In traditional manufacturing, inspection typically happens after the production process is complete. However, with laser tracking systems, measurements can be taken during the manufacturing process, allowing for real-time quality control. This helps catch issues early, reducing the need for costly rework.
2. Automated Reporting
Modern laser tracking systems can be integrated with automated reporting software, allowing manufacturers to generate detailed reports quickly. These reports can track measurement trends, highlight areas of concern, and serve as a basis for decision-making and process improvement.
3. Integration with CAD Models
Laser trackers can be paired with CAD (Computer-Aided Design) models to ensure that the final product matches the design specifications. This integration helps compare the physical measurements with the digital models in real-time, ensuring complete alignment.
For manufacturers looking to integrate laser tracking with CAD systems, Expert Technologies Group offers solutions that streamline the process, ensuring seamless data exchange and faster quality checks.
Applications of Laser Tracking Systems in Quality Control
Laser trackers are used across various industries, each benefiting from their precision and flexibility. Here are a few key applications:
1. Aerospace Industry
In the aerospace industry, laser tracking systems ensure that parts such as fuselages, wings, and engine components meet the strict tolerances required for safe and efficient flight. Even small misalignments in these parts can cause significant issues, making quality control a critical part of the manufacturing process.
2. Automotive Manufacturing
For the automotive industry, laser tracking systems ensure that body panels, engine parts, and structural components fit together perfectly. Manufacturers use laser trackers to maintain tight tolerances, improve assembly line efficiency, and ensure the quality of each vehicle.
3. Heavy Equipment Manufacturing
In heavy equipment manufacturing, large-scale measurements are crucial for ensuring that large components such as cranes, tractors, and excavators are built to precise specifications. Laser tracking systems are used to measure the alignment and assembly of these large parts, helping to prevent costly errors and downtime.
4. Shipbuilding
Laser trackers are invaluable in shipbuilding, where accuracy in the alignment of massive structures is crucial. These systems ensure that ship parts, such as hulls and decks, are properly aligned during assembly, which is essential for ensuring the structural integrity of the vessel.
Advantages Over Traditional Measurement Methods
Laser tracking systems offer several advantages over traditional measurement techniques, such as dial indicators, calipers, and coordinate measuring machines (CMMs). Here’s how laser trackers outshine older methods:
1. Greater Flexibility
Laser tracking systems are highly adaptable, capable of measuring large objects and hard-to-reach areas that would be difficult for traditional measuring instruments to access. This flexibility is especially useful in industries with complex and varied geometries.
2. Improved Data Collection
While traditional tools provide limited data, laser tracking systems generate a wealth of information. With the ability to capture thousands of data points per second, manufacturers can create highly accurate digital models of components for further analysis.
3. Cost-Effectiveness
Although the initial investment in a laser tracker can be higher, the long-term savings are substantial. By reducing the need for manual inspection and minimizing errors, laser tracking systems ultimately save manufacturers time and money by increasing production efficiency and reducing rework.
Laser Tracking Systems and Their Impact on Product Quality
One of the most important benefits of using laser tracking systems is their ability to consistently ensure high product quality. By measuring parts with extreme accuracy, manufacturers can detect issues that may otherwise go unnoticed. This leads to fewer defects and higher-quality products, which in turn helps improve customer satisfaction.
Moreover, laser tracking systems help manufacturers meet regulatory requirements and industry standards, ensuring compliance with quality certifications and audits.
The Future of Laser Tracking in Quality Control
As technology continues to evolve, laser tracking systems are becoming even more advanced. Future developments could include:
-
Integration with AI: Artificial intelligence can analyze data from laser trackers to predict potential issues and suggest improvements.
-
Advanced data analytics: The increasing use of data analytics will enable manufacturers to gain deeper insights into their production processes and optimize operations in real time.
-
Increased portability: Newer models of laser trackers are becoming smaller, lighter, and easier to transport, making them more versatile for on-site inspections.
Conclusion
Laser tracking systems are revolutionizing the way manufacturers approach quality control. Their ability to deliver high-precision measurements in real-time helps companies improve product quality, reduce errors, and increase operational efficiency. As industries continue to push for higher standards and faster production timelines, the role of laser tracking systems will only become more crucial.