What to Know Before Integrating Industrial Automated Tools in Your Plant
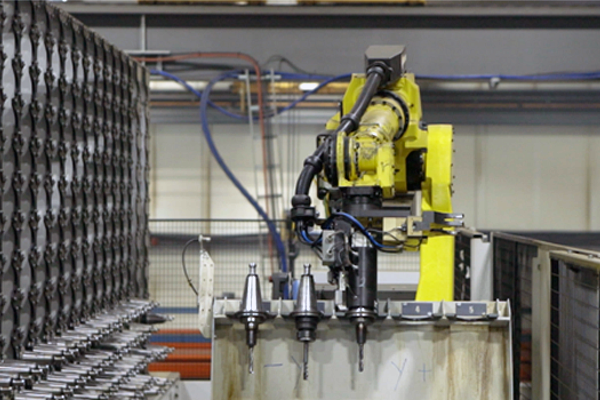
Industrial Automated Tools
Thinking about taking the leap into automation? Great choice—but hold up. Before diving in, there are a few things you really need to know to make the transition smooth, cost-effective, and successful.
Automation can transform your operations, but only when done right. Let’s break down everything you should consider before installing Industrial Automated Tools in your plant.
Why Industrial Automation is a Game-Changer
Automating your plant isn’t just about following trends—it’s about staying competitive. From improving productivity to reducing errors, industrial automation gives your operations an edge. Tools like robotic arms, CNC machines, smart sensors, and automated guided vehicles (AGVs) help businesses meet increasing demands with precision and consistency.
But here’s the catch: if you don’t plan the integration properly, these tools could cost more than they save. So let’s cover the groundwork.
Start With a Clear Objective
Before buying equipment or calling in vendors, ask yourself: Why are we automating?
Maybe you’re trying to:
-
Reduce labor costs
-
Improve product consistency
-
Minimize downtime
-
Meet production goals faster
Knowing your objective helps you choose the right industrial automated tools and avoid wasting money on tech you don’t need.
Understand Your Plant’s Current Capabilities
Take a good look at your current setup. Is your facility even ready for automation?
You’ll need to assess:
-
Electrical infrastructure
-
Floor space and layout
-
Data systems and network capabilities
-
Workforce readiness
If your plant lacks the foundation, you’ll need to upgrade first. This might mean rewiring, redesigning workflows, or even retraining your staff.
Choose the Right Tools for the Job
Not all tools are created equal. Some are perfect for repetitive tasks, others for high-precision manufacturing. Choosing the right one depends on your processes.
For example:
-
Robotic arms are ideal for pick-and-place or welding.
-
Vision systems help with inspection and quality control.
-
AGVs transport materials across the plant floor.
-
PLC controllers manage and monitor the automation process.
Want a detailed breakdown of which tools suit your needs? Check out this excellent resource on industrial automated tools and their use cases.
Plan for Scalability
Don’t just automate for today—think long-term.
You might only need a few machines now, but what happens when production doubles next year? Choose tools and software platforms that allow for easy expansion. Look for modular systems that can scale without massive overhauls.
Safety Should Be Non-Negotiable
With automation comes new safety concerns. Machines don’t have instincts—they just follow commands.
Make sure you implement:
-
Safety interlocks
-
Emergency stop buttons
-
Light curtains or motion sensors
-
Clear safety protocols for workers
Integrating automation without a solid safety strategy can lead to injuries, downtime, and legal issues.
Budget Wisely—It’s Not Just Equipment Costs
It’s easy to focus on the price tag of the equipment itself, but don’t forget:
-
Installation and integration costs
-
Software licensing
-
Maintenance and servicing
-
Employee training
-
Downtime during the switch
Create a full budget that includes the entire lifecycle of the tools. You’ll avoid surprises later and make smarter ROI projections.
Train Your Team Early
No matter how advanced your automation is, it won’t help much if your team doesn’t know how to use it.
Start training programs before the tools even arrive. Help your operators, engineers, and maintenance crew understand the system, troubleshoot common issues, and stay productive.
Also, consider upskilling workers who might otherwise be replaced. That’s not just good ethics—it’s good business.
Data Integration is Key
Automation produces tons of valuable data—but only if you know how to use it.
Make sure your automated tools can connect to your plant’s ERP or MES systems. This allows real-time monitoring, predictive maintenance, and smarter decision-making.
Systems with built-in IoT support or cloud connectivity offer the best bang for your buck.
Work With the Right Automation Partner
You don’t have to go it alone. A good automation partner helps you navigate hardware choices, system design, implementation, and support.
Look for:
-
Industry experience
-
Strong technical support
-
Customization capabilities
-
Positive client reviews and case studies
Partnering with experts ensures you get a system that fits your unique operation—not a one-size-fits-all solution.
Common Pitfalls to Avoid
Here are a few mistakes many companies make (so you don’t have to):
-
Skipping feasibility studies: Always test before you invest.
-
Underestimating downtime: Expect some disruption—and plan for it.
-
Focusing only on the machine: Consider the whole system, including workflows and operators.
-
Neglecting maintenance: Automation still needs regular check-ups.
Avoiding these traps can save you from costly delays or failed implementations.
Final Thoughts: Automation Done Right Pays Off
There’s no question—industrial automated tools can totally transform your plant. But success depends on preparation. Know your goals, understand your infrastructure, plan for growth, and don’t cut corners on safety or training.
When done right, automation leads to higher efficiency, better quality, lower costs, and happier employees.
Need help figuring out where to start? Reach out to a specialist or browse through expert services that provide tailored solutions in automation. The future of manufacturing is here—just make sure you’re ready for it.