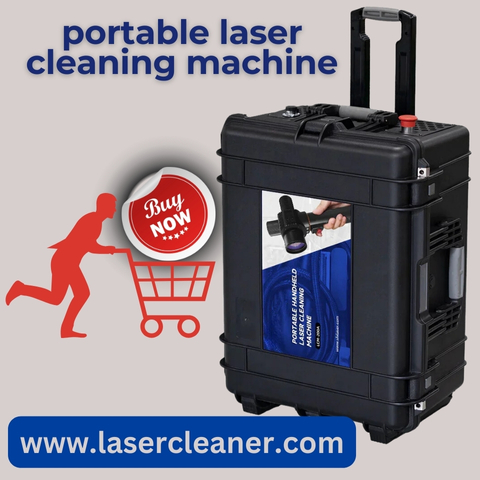
In industrial maintenance and surface preparation, the choice of tools can directly impact productivity, safety, and operational cost. One piece of equipment that’s steadily becoming a preferred option in numerous sectors is the portable laser cleaning machine. While traditional cleaning methods—such as sandblasting, chemical cleaning, or mechanical abrasion—have been in use for decades, industries that demand precision, minimal downtime, and high-quality results are shifting their attention toward laser technology.
This guide explores in-depth why certain industries are favoring this method, where it is being used, and how its unique operational mechanics make it a powerful addition to modern manufacturing and restoration workflows.
The Core Working Principle of Portable Laser Cleaning Machine
A portable laser cleaning machine works on the principle of laser ablation. When the laser beam hits the surface, the contaminants (like rust, paint, or grease) absorb the energy and are instantly evaporated or vaporized without damaging the base material. Unlike abrasive or chemical methods, the energy is focused and controlled—resulting in targeted cleaning.
Portability means that the machine is compact, easy to move, and suitable for field work or locations where fixed installations are not feasible. Operators can carry the device to pipelines, historical monuments, automotive parts, or machinery components, cleaning surfaces that are otherwise hard to access using traditional techniques.
Where Portable Laser Cleaning Machines Are in High Demand
Several industries are actively integrating portable laser cleaning machines into their operations. Below are the most prominent ones:
1. Automotive Manufacturing and Restoration
The automotive sector deals with parts that require degreasing, rust removal, and paint stripping. Whether it’s restoring a classic car or preparing new parts for coating, laser cleaning offers non-contact and non-abrasive preparation. Portable machines are used to treat chassis, engine components, and even wheels on-site.
2. Aerospace Component Maintenance
Precision and material integrity are critical in aerospace. The portable design allows technicians to clean parts without dismantling them, especially in cases where surface coatings or contaminants could affect aerodynamics or structural stability. The laser removes contaminants while preserving the original material surface.
3. Shipbuilding and Offshore Platforms
Ships are prone to rust due to constant exposure to seawater. Traditional rust removal requires heavy machinery or chemicals, both of which can be time-consuming and hazardous. Portable laser cleaning machines allow shipyard teams to access and clean difficult parts of the hull or propellers—even underwater bases—with mobility and precision.
4. Power Plants and Nuclear Facilities
In energy production environments, cleaning is not just about appearance—it’s about safety and operational efficiency. Nuclear power plants, for instance, require non-contact, residue-free cleaning solutions. A portable laser system can be used on reactor components, pipes, and sensitive metal structures without generating secondary waste.
5. Tool and Die Industry
In mold-making, any imperfection—like burnt-on plastic or carbon buildup—can cause major defects in the final product. Portable lasers clean molds in place without the need to uninstall them, which keeps operations efficient and minimizes tool wear.
What Makes It Suitable for Precision Workflows
The key to the effectiveness of a portable laser cleaning machine lies in its adjustability and control. Parameters like pulse duration, energy density, and beam size can be tailored to the material and contaminant type. This means operators can clean fragile materials like copper or sensitive electronics without damaging the surface.
Moreover, there is no need for consumables like abrasives or solvents, which simplifies logistics and reduces dependency on external supplies. In industries where compliance and traceability are essential (such as medical devices or defense), laser cleaning ensures consistency and repeatability.
Maintenance Requirements and Operational Insights
Operating a portable laser cleaning machine does not require extensive mechanical adjustments. However, users need to maintain the following:
-
Laser Optics Inspection: Periodically check and clean lenses to ensure optimal beam quality.
-
Cooling System Management: The built-in cooling mechanism (often air or water-cooled) must be monitored to prevent overheating.
-
Software Calibration: Ensure software settings are matched to the material being cleaned for optimal results.
-
Protective Equipment Use: Operators must wear laser safety glasses and ensure the work environment is compliant with Class IV laser safety standards.
Training is often short-term, and with digital interfaces, most modern systems are plug-and-play. Technicians can quickly adapt to usage even with minimal technical background, especially if the machine includes presets for common materials.
Environmental and Regulatory Compliance
One reason portable laser cleaning machines are gaining traction is their alignment with modern environmental standards. Since they don’t use solvents, acids, or abrasive media, there’s no secondary pollution. This is especially important in regions with strict environmental laws or zero-waste mandates.
Additionally, because there’s minimal residue, waste management costs are significantly reduced. Some models are equipped with fume extractors that filter out particles during laser operation, further enhancing environmental safety.
ROI Considerations and Long-Term Integration
While the upfront investment for a portable laser cleaning machine may be higher than manual methods, industries often look at total cost of ownership. Factors influencing ROI include:
-
Reduced Downtime: Cleaning tasks are completed faster, allowing equipment to return to service quickly.
-
Minimal Consumables: No need to purchase and store chemical agents or blasting media.
-
Operator Efficiency: Less fatigue and higher output due to lightweight handheld designs.
-
Longevity of Assets: Non-damaging cleaning extends the life of machinery and components.
Most businesses see payback within the first few months to a year depending on usage frequency. In high-volume manufacturing or maintenance environments, this window shortens further.
Use Cases That Reinforce Industrial Demand
Some specific applications further illustrate how diverse the need for a portable laser cleaning machine can be:
-
Restoration of Historical Sites: Removing soot, oxidation, or biological growth from monuments without damaging inscriptions or underlying stone.
-
Weld Preparation: Pre-weld cleaning to remove oxides and post-weld cleaning to remove soot, improving weld integrity.
-
Pipeline Maintenance: Mobile units are taken to remote oil rigs or gas lines for degreasing and preparation.
-
Railway Infrastructure: Cleaning train axles, couplers, and platforms exposed to environmental grime and rust.
-
Injection Molding: Non-destructive mold cleaning between production cycles to prevent downtime.
These use cases prove that the technology is more than just innovative—it is actively resolving real-world industrial challenges.
Final Thoughts
The move toward a portable laser cleaning machine is not merely a trend—it is a calculated shift driven by precision, efficiency, and compliance. Whether it’s maintaining aerospace parts or cleaning factory molds without disassembly, the application spectrum is wide and growing. As industries continue to prioritize safety, speed, and sustainability, adopting laser cleaning is becoming less of an option and more of a necessity. The portability factor just makes the technology that much more accessible, especially in environments where flexibility is essential.